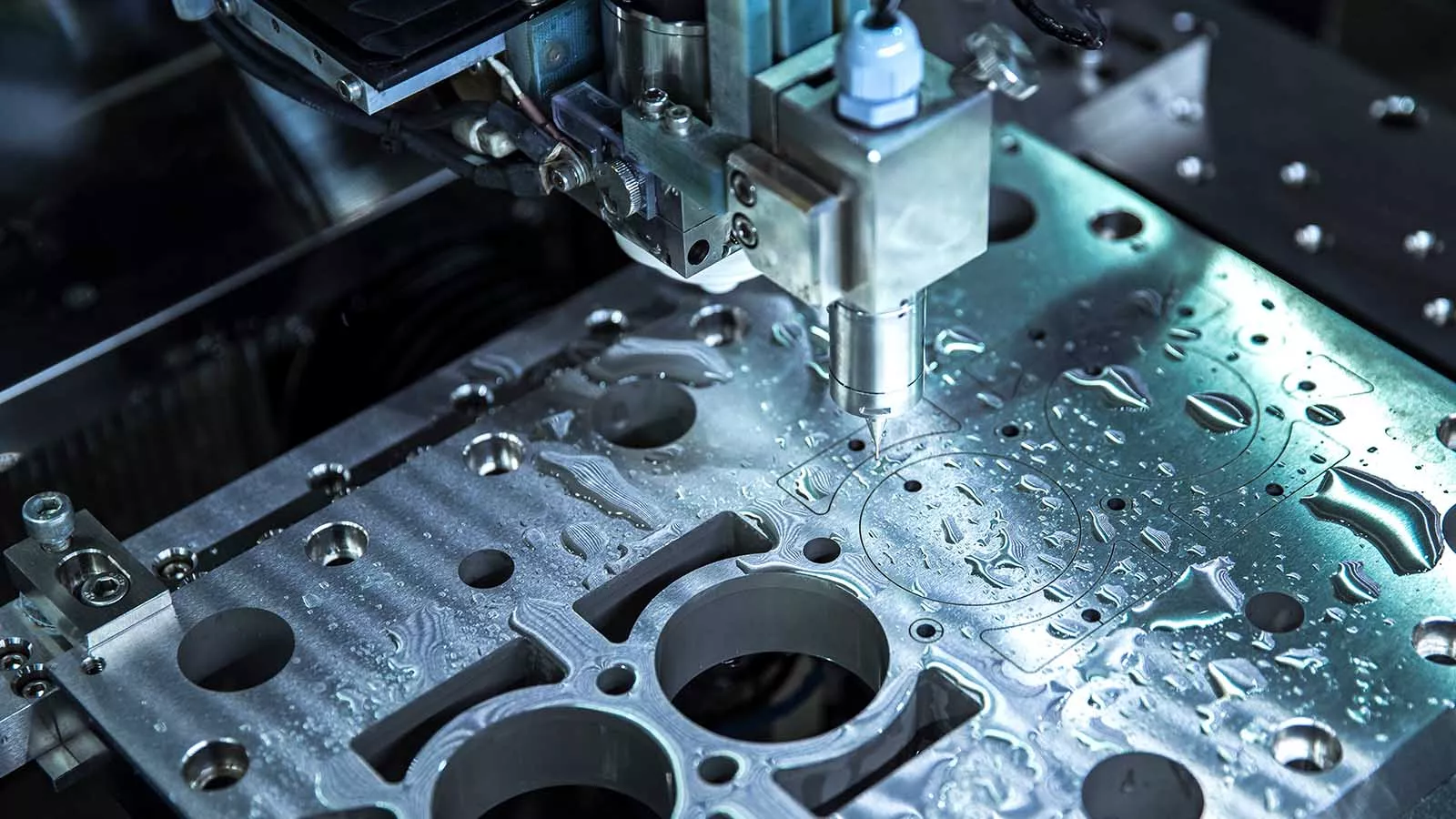
Surface Finish
Grinding
Grinding is a finishing process that uses an abrasive wheel to achieve extremely smooth surfaces or precise geometrical shapes on the workpiece.
Technical Characteristics
Grinding is characterized by its ability to achieve high precision and surface quality, often reaching finishes as smooth as 0.1 μm Ra. It’s the go-to method for parts requiring tight tolerances that milling and turning cannot achieve.
Materials and Applications
Ideal for hard materials like hardened steel, ceramics, and carbides, grinding is extensively used in tool manufacturing, automotive, and aerospace industries, where precision and surface integrity are non-negotiable.
Pros and Cons
Grinding offers unmatched precision and surface quality, making it essential for many high-precision applications. The downside is its relatively slow speed and the higher cost associated with the process due to the wear and maintenance of the abrasive wheels.
Sanding
Sanding uses abrasive materials to smooth surfaces, typically as a finishing step to remove minor imperfections left by prior machining processes.
Technical Characteristics
Sanding is versatile, allowing for adjustment in grit size to move from rough to fine finishes. It’s often used in combination with other finishing processes to prepare surfaces for painting or coating.
Materials and Applications
Sanding is suitable for a wide range of materials, including wood, metals, and plastics. It’s commonly used in the automotive and furniture industries to prepare surfaces for final finishing.
Pros and Cons
The primary advantage of sanding is its simplicity and effectiveness in achieving a smooth finish. However, it can be labor-intensive and time-consuming, especially for parts with complex geometries or requiring ultra-smooth finishes.
Bead Blasting
Bead blasting is a mechanical process that involves propelling a stream of abrasive glass beads at high speed against the surface of a part. This action effectively removes surface imperfections, resulting in a uniform, matte finish that can enhance the part’s aesthetic and functional properties.
Materials and Applications
Bead blasting is versatile, applicable to a wide range of materials including metals like aluminum, steel, and titanium, as well as plastics. It’s commonly used in the automotive, aerospace, and electronics industries to prepare surfaces for painting, anodizing, or simply to improve their appearance.
Pros and Cons
The main advantage of bead blasting is its ability to provide a consistent, aesthetically pleasing finish that can also obscure minor surface defects. However, it’s important to control the blasting process carefully to prevent material removal that could alter the part’s dimensions or introduce surface stresses.
Polishing
Polishing is a finishing process that uses abrasives or chemical agents to achieve a high-gloss, mirror-like finish on the surface of a part. It’s a method that not only enhances the part’s visual appeal but can also reduce friction, improve cleanliness, and increase corrosion resistance.
Materials and Applications
This method is ideal for metals such as stainless steel, aluminum, and brass, and is widely used in the medical, food processing, and luxury goods industries, where a high degree of surface finish is essential for both aesthetic and functional reasons.
Pros and Cons
Polishing offers the benefit of a smooth, reflective surface that enhances the part’s visual appeal and performance characteristics. However, it can be labor-intensive and time-consuming, especially for parts with complex geometries or requiring extremely high finishes.
Brushing
Brushing uses fine bristles or abrasive media to create a uniform, directional texture on the surface of a part. This method is particularly effective for highlighting the natural luster of metal parts without achieving the high gloss of polishing.
Materials and Applications
Suitable for a variety of metals, including aluminum, stainless steel, and copper, brushing is often employed for architectural components, consumer electronics, and automotive parts, where a satin finish is desired.
Pros and Cons
Brushing is advantageous for its ability to provide a consistent, aesthetically pleasing finish that can conceal fingerprints and minor imperfections. However, it might not be suitable for applications requiring a non-directional finish or where surface smoothness is a critical factor.
Tumbling and Vibratory Finishing
Tumbling and vibratory finishing are batch processes that smooth and polish parts by placing them in a container filled with abrasive media and either rotating the container (tumbling) or vibrating it (vibratory finishing). These methods are excellent for processing large quantities of small parts.
Materials and Applications
These processes are applicable to a broad range of materials, including metals, plastics, and ceramics. They are particularly useful in the automotive, aerospace, and jewelry industries for deburring, smoothing, and polishing components.
Pros and Cons
The primary advantage of tumbling and vibratory finishing is their efficiency in finishing large batches of parts simultaneously, providing a uniform finish. The main drawback is the potential for part-on-part contact, which can lead to damage or deformation, especially for delicate parts.
Media Blasting
Media blasting is a versatile finishing process that involves propelling a stream of abrasive material against the surface of a part under high pressure. This method is highly effective for cleaning, deburring, and finishing surfaces.
Materials and Applications
Media blasting can be applied to a wide range of materials, including metals, plastics, and composites. It’s particularly useful in preparing surfaces for subsequent coatings, removing manufacturing residues, or creating a specific surface texture. Common applications include automotive parts, aerospace components, and industrial machinery.
Pros and Cons
The main advantage of media blasting lies in its ability to uniformly finish complex geometries and reach difficult-to-access areas. However, it requires careful selection of blasting media and parameters to avoid damaging the substrate or altering critical dimensions.
Vapor Polishing
Vapor polishing is a finishing technique that uses a chemical vapor to melt the surface of plastic parts, resulting in a smooth, glossy finish. This method is particularly suited for materials that are difficult to polish mechanically.
Materials and Applications
Vapor polishing is primarily used on thermoplastics such as polycarbonate, ABS, and acrylic. It’s ideal for applications requiring optical clarity or a high-gloss finish, such as medical devices, automotive lights, and display cases.
Pros and Cons
Vapor polishing offers the advantage of achieving a clear, smooth finish without introducing mechanical stress to the part. However, it involves the use of hazardous chemicals, requiring strict safety measures and environmental controls.
Knurling
Knurling is a process that creates a patterned texture on the surface of a part, usually for grip enhancement or aesthetic purposes. It involves pressing a patterned tool against the rotating workpiece to form a tightly controlled, uniform pattern.
Materials and Applications
Knurling is commonly performed on metal parts, including aluminum, steel, and brass. It’s widely used in tool handles, control knobs, and custom fasteners where an improved grip or decorative finish is desired.
Pros and Cons
The primary benefit of knurling is its ability to enhance the tactile properties of parts without significantly impacting their dimensional tolerances. However, it’s limited to accessible, rotationally symmetrical areas and may require additional finishing steps to remove any burrs or sharp edges created during the process.
Powder Coating
Powder coating is a dry finishing process where a powder material is electrostatically applied to a surface and then cured under heat to form a hard, protective layer.
Technical Characteristics
This process stands out for its ability to produce a thick, uniform coating without runs or sags, offering excellent durability and resistance to chipping, scratching, and corrosion. The range of available colors and finishes, from matte to high gloss, allows for significant aesthetic versatility.
Materials and Applications
Powder coating is predominantly used on metal surfaces, including steel, aluminum, and brass, making it a popular choice for automotive parts, outdoor furniture, and industrial equipment. Its robust nature ensures components withstand harsh environments and heavy use.
Pros and Cons
The advantages of powder coating include its environmental friendliness, emitting fewer volatile organic compounds (VOCs) than liquid coatings, and its durability. However, its application requires specialized equipment and cannot be easily applied to non-conductive materials.
Anodizing
Anodizing is an electrochemical process that enhances the natural oxide layer on the surface of metal parts, primarily aluminum. This method increases corrosion resistance, surface hardness, and wear resistance, while also allowing for the addition of colored dyes for aesthetic purposes.
Technical Characteristics
Anodizing involves immersing the aluminum part in an acid electrolyte bath and passing an electric current through the medium. This process thickens the natural oxide layer, making it more durable and resistant to corrosion.
Materials and Applications
Primarily used for aluminum, anodizing is ideal for aerospace, automotive, consumer electronics, and architectural applications where durability and cosmetic appearance are crucial.
Pros and Cons
Anodizing offers excellent corrosion and wear resistance, improved adhesion for paint primers, and aesthetic enhancement. However, it is limited to aluminum and its alloys and requires strict control over the electrolytic process to ensure uniformity and quality of the finish.
Thermal Finishing Methods
Thermal finishing methods involve the use of heat or thermal energy to alter the surface properties of machined parts, improving their mechanical and physical characteristics.
Laser Engraving
Laser engraving is a non-contact thermal process that uses a laser beam to remove material from the surface of a part, creating permanent marks without affecting the part’s structural integrity.
Technical Characteristics
This method provides high precision and repeatability, allowing for intricate designs and legible markings on a variety of materials.
Materials and Applications
Suitable for metals, plastics, ceramics, and even wood, laser engraving is widely used for serial numbers, logos, and custom designs in industries ranging from medical devices to automotive manufacturing.
Pros and Cons
Laser engraving offers unmatched detail and precision, with the ability to mark almost any design. However, it can be limited by the material’s ability to absorb the laser energy, and the depth of engraving is generally shallow.
Heat Treating
Heat treating encompasses various processes used to alter the microstructure of materials, enhancing their mechanical properties such as strength, hardness, and ductility.
Technical Characteristics
Common heat treating processes include annealing, tempering, case hardening, and through hardening, each tailored to specific material requirements and desired outcomes.
Materials and Applications
Widely applicable to steel and other alloys, heat treating is essential in automotive, aerospace, and tool manufacturing, where enhanced material properties are critical for performance and durability.
Pros and Cons
Heat treating can significantly improve a part’s mechanical properties, making it more suitable for demanding applications. However, it requires precise control over temperature, time, and atmosphere to achieve consistent results and can sometimes lead to distortion if not properly managed.